Author: Eniko Zsoldos, PhD – Senior Scientist, Cell R&D at NOVONIX
Introduction to Sodium Ion Batteries (SIB)
After three decades of steadily falling lithium-ion battery (LIB) costs, 2022 marked a historic reversal—cell prices rose significantly due to surging lithium raw material costs. This supply chain volatility prompted the battery industry to seriously explore alternatives, with sodium-ion batteries (SIBs) emerging as a front-runner.
SIBs offer compelling advantages compared to LIBs:
- Lower-cost raw materials (Sodium vs. Lithium)
- More sustainable, Earth-abundant metals in the cathode materials and in the current collectors (Fe, Mn, Al vs. Ni, Co, Cu)[1]
- Geographically diversified raw material distribution for better supply chain resilience[1]
- Excellent rate capability, especially in Prussian Blue Analogs
- Superior low-temperature performance
- Improved safety in certain chemistries (e.g., NFPP)
- Ideal for stationary energy storage (BESS), with potential for EV applications
- Drop-in replacement compatibility with existing LIB gigafactories
Currently, SIBs cost about $125/kWh, but a technoeconomic study by Yao et al.[2] suggests costs could fall to $30/kWh by 2045, as shown in Figure 1. This opens a vast opportunity for innovation in all aspects of SIB production. In contrast, LIBs are approaching their minerals cost floor, limiting further gains through traditional scale-up.
Although LIB prices have fallen sharply since 2023, the potential benefits of SIB chemistries, including sustainability and supply chain instability, maintain their position as a strong complement to LIBs for many applications.
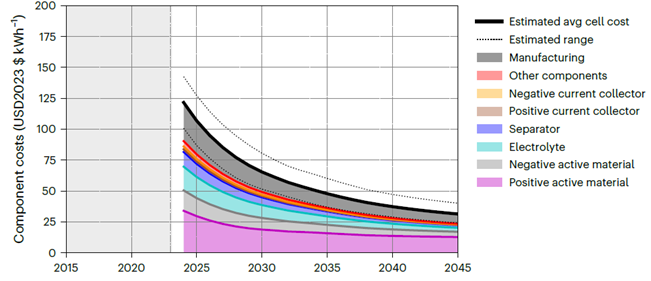
Market Trends
The performance characteristics of SIBs position them to compete with lithium iron phosphate (LFP) cell chemistry in similar applications that require low-cost batteries, with an acceptable trade-off in lower energy density. Example markets include battery energy storage systems (BESS), data center back-up storage, and low to mid-range EV markets.
Although today’s SIB costs ($125/kWh) are not yet competitive with LFP, ($50 – 70/kWh), projections show that SIBs could surpass LFP in cost-effectiveness between 2032 and 2047. This wide range reflects uncertainties in mineral pricing, demand growth, and geopolitical supply chain disruptions. Companies that invest in R&D today will be best positioned to remain competitive tomorrow. The last two decades in battery manufacturing were defined by LIB scale-up. Since a vast knowledge base and infrastructure is now in place, commercialization of SIBs is coming fast, with mass manufacturing already scaling in China, based on announcements by CATL, BYD, and others[3], [4].
The best time to start your SIB R&D was yesterday. The second-best time is today—with NOVONIX R&D Services.
Sodium-Ion Battery Active Materials Overview
Cathode Materials
- Layered Oxides (e.g., NFM – NaNi₁/₃Fe₁/₃Mn₁/₃O₂)
- Highest energy density of the SIB cathode materials but has trade-offs due to the higher cost caused by Nickel content. These materials are analogous to NMC materials in the LIB battery space.
- Common dopants include Mg, Ti, Cu, Zn, Ca to enable electrochemical stability and exposure to moisture during manufacturing[5].
- Polyanion Cathodes (e.g., NFPP – Na4Fe3(PO4)2(P2O7) or NVPF – Na3V2(PO4)2F3)
- Lower capacity and lower voltage than the layered oxides, but better safety performance and lower cost. These materials are analogous to LFP in the LIB space.
- Prussian Blue Analogs (e.g., PBA – NaₓMnFe(CN)₆)
- Highest rate capable material in the sodium ion space with >10C discharge rates[1]. Trade-off is they are the lowest energy density SIB cathode.
Anode Materials
- Hard Carbon (HC)
- The dominant anode material in SIB, with properties that are highly dependent on the carbon material precursor.
- Alloying Materials (e.g., Sn, Pb, P)
- High energy density anode materials that alloy with Na, but they experience large volume changes upon sodiation (>350%) leading to poor cycling stability and lifetime[5]. These materials are analogous to silicon anodes in the lithium-ion space but are lower in technology readiness level.
- Anode-Free Designs
- The highest theoretical energy density anode in SIB. However, like LIB anode-free and solid-state chemistries, they are the farthest from commercialization on this list, with significant safety issues to be overcome in research.
Examples of the three most common SIB materials are shown in Figure 2, plotting the first cycle voltage vs capacity. These are Na-ion coin half cells made at NOVONIX Battery Testing Solutions (BTS).
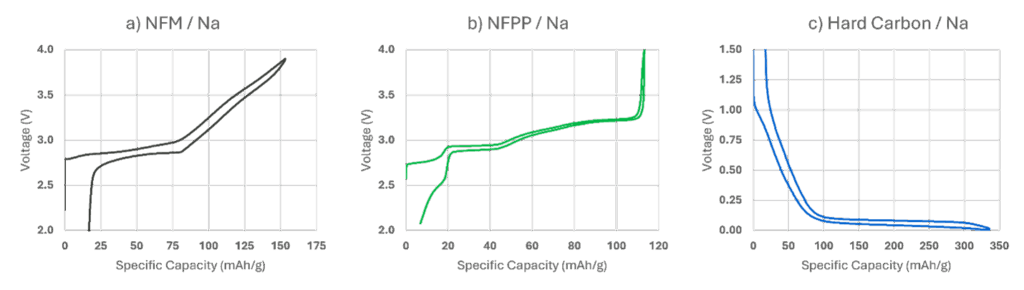
Core Challenges Facing SIB Development
Despite strong sustainability, cost and supply chain advantages, SIBs still face real technical hurdles. The biggest challenge is low cell energy density, both volumetric (272 Wh/L) and gravimetric (134 Wh/kg), due to lower voltages and lower specific capacities than LIB materials[2]. There are also challenges with air stability and moisture uptake, depending on the active material used. Additionally, NFM materials are currently expensive because they contain ~30% Ni, so the expected industry trend is to reduce the nickel content over the coming years.
Furthermore, there are challenges associated with the electrochemical stability window of the materials: they are limited to a lower full cell voltage because of 0.3 V difference between Na/Na+ vs Li/Li+[1]. This means that degradation reactions on the cathode side, such as lattice oxygen release, electrolyte oxidation, transition metal dissolution occur at a lower voltage than in lithium-ion cells.
Overcoming these issues requires deep scientific insight and engineering innovation—areas where NOVONIX can provide critical support:
- Our R&D Services can help you rapidly demonstrate your technology in pouch and cylindrical cells, leveraging our experience and team of battery scientists, engineers, and technicians.
- NOVONIX Ultra-High Precision Coulometry (UHPC) cell testing equipment enables rapid cycles of development in areas such as active material scale-up, electrolyte optimization, cell design, and more.
Sodium-ion Development at NOVONIX BTS
NOVONIX Battery Technology Solutions provides prototyping services, including:
- Slurry mixing
- Electrode coating
- Cell assembly
- Electrolyte filling
- Formation
- Long-term cycle testing
- Accelerated testing via UHPC
- Post-mortem analysis
If there is a SIB material of interest to you (anode, cathode, inactive component) NOVONIX Battery Technology Solutions can build prototype cells to accelerate your R&D. We offer tailor made prototyping services to each customer, such that you can enter or exit at any point in the cell line process. We can ship you coated electrodes, dry cells, or filled cells after formation, in any combination to suite your business and research needs. Our team of battery scientists and engineers work with your team to analyse and understand your results, leveraging our expertise to drive your technology forward. In addition to thousands of standard precision battery testing equipment, we also use our own UHPC equipment in our Service programs. These measurements enable rapid detection of material performance differences and give insight into the electrochemical degradation mechanisms that are occurring. Learn more about UHPC measurements from Stephen Glazier, Director, Cell Technology.
Figure 3 shows a set of SIB pouch cells built at NOVONIX tested on UHPC equipment. In this specific cell design, the cells made with an NFPP cathode deliver a higher CE than the cells built with an NFM cathode. These SIB pouch cells are tested with precise measurements for CE, charge endpoint slippage, and fade rate. These early insights enable faster R&D for SIB technology to understand the effects and trade-offs associated with different cell designs. Some example variables to test can include upper cutoff voltage, electrolyte composition, and active material loadings.
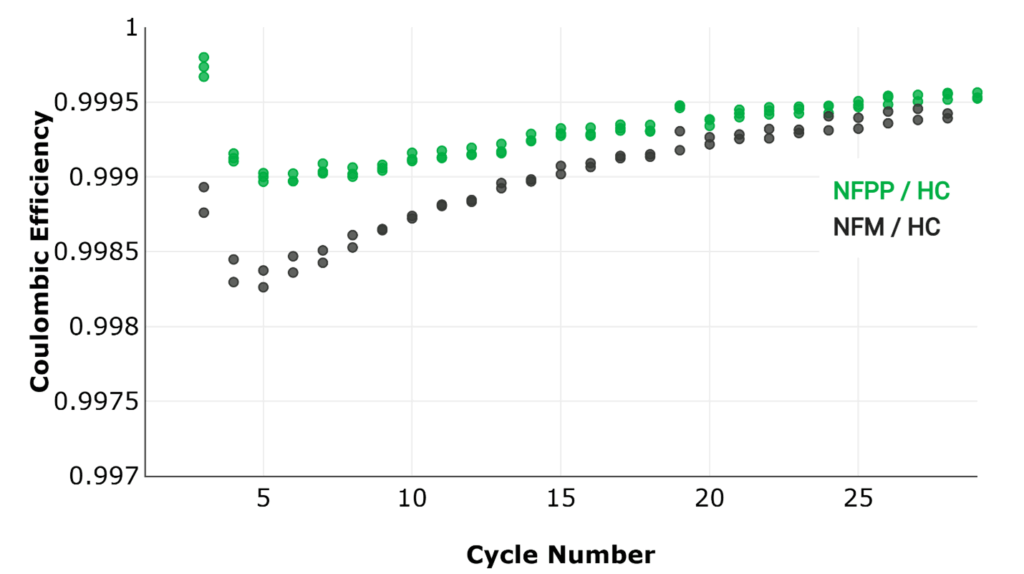
Identical SIB pouch cells were also tested in long term cycling aging at 40°C. Figure 4 shows the normalized discharge capacity retention as a function of cycle number. The NFPP / HC pouch cells in this design show better capacity retention compared to NFM / HC, as predicted by the CE measurements as early as cycle 5! This highlights the importance of using UHPC systems for early detection of precise CE to enable fast iteration during R&D for sodium ion batteries. It is also worth noting that the y-axes are magnified in both Figure 3 and Figure 4, with the CE > 0.999, and the capacity showing less than 2% fade after 100 cycles.
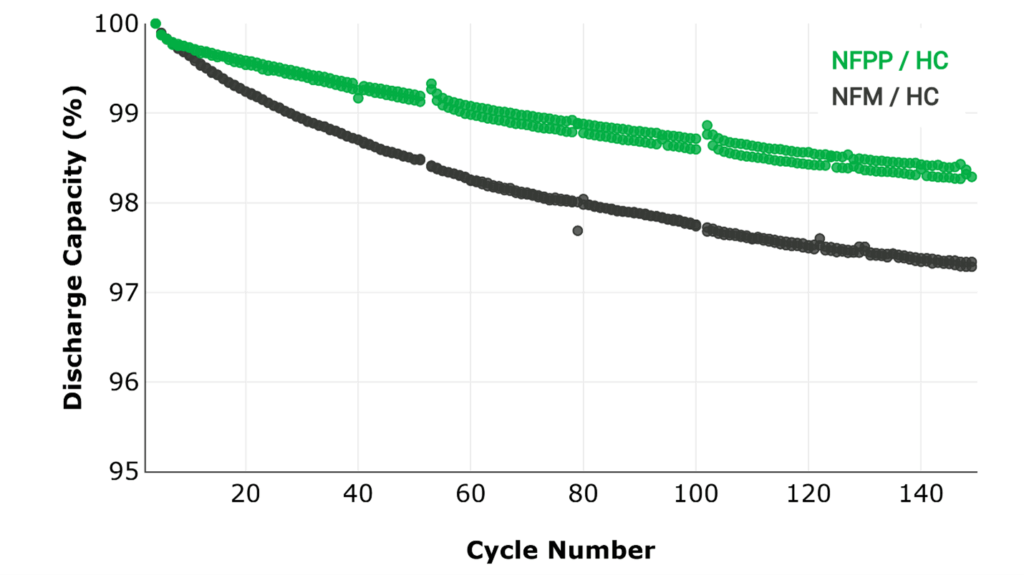
Why Strategic R&D is the Real Cost Driver
The industry can’t just rely on market penetration and economies of scale to drive down the cost of sodium ion batteries. While LIB gigafactories can adapt to SIB manufacturing with minimal changes, breakthroughs in energy density and cell design will be the real game-changers. Technoeconomic modelling by Yao et al [2] shows that even an aggressive manufacturing “learning rate” of 20% for sodium ion cathodes, anodes and electrolytes will have minimal effect on projected cell prices. Instead, design improvements related to increasing energy density have the highest likelihood for driving down sodium ion cell prices and accelerating market adoption. Some examples of ways to increase energy density include increasing: electrode loading, upper cutoff voltage, and specific capacity.
By partnering with NOVONIX BTS, you gain access to the tools and expertise needed to move faster, design smarter, and compete effectively in the sodium-ion future.
Testing Available for SIB Prototyping at NOVONIX
- Active Materials
- NFPP
- NFM (various compositions and suppliers)
- Hard Carbon (various suppliers)
- Cell Types
- Na coin half cells
- Single layer pouch full cells (SLP)
- Multilayer wound and stacked pouch cells (200 mAh to 5 Ah)
- Electrolyte
- Carbonate solvents EC, PC, DEC, DMC
- Other solvents such as ethers DME, glymes, amides
- Salts NaPF6, NaFSI, NaTFSI, NaClO4
- A variety of additives
- Failure Mode Analysis
- Long term cycling using various test protocols (C rates, temperatures)
- UHPC (precise CE, charge endpoint slippage and fade)
- Differential voltage analysis (dQ/dV)
- Chemical and structural analysis (SEM, XRD, GC-MS, XRF, ICP)
Note that these are only our current materials at the time of writing this blog post. To get up to date information on our sodium ion materials availability for your cell builds of interest, please contact us and we will be happy to discuss options and pricing.
References
- L. Zhao et al., “Engineering of Sodium-Ion Batteries: Opportunities and Challenges,” Engineering, vol. 24, pp. 172–183, May 2023, doi: 10.1016/j.eng.2021.08.032.
- A. Yao, S. M. Benson, and W. C. Chueh, “Critically assessing sodium-ion technology roadmaps and scenarios for techno-economic competitiveness against lithium-ion batteries,” Nat. Energy, vol. 10, no. 3, pp. 404–416, Jan. 2025, doi: 10.1038/s41560-024-01701-9.
- CATL, “Naxtra Battery Breakthrough & Dual-Power Architecture: CATL Pioneers the Multi-Power Era,” CATL. [Online]. Available: https://www.catl.com/en/news/6401.html
- C. Murray, “BYD launches sodium-ion grid-scale BESS product,” Energy Storage News. [Online]. Available: https://www.energy-storage.news/byd-launches-sodium-ion-grid-scale-bess-product/
- Y. Wu et al., “Recent Progress in Sodium-Ion Batteries: Advanced Materials, Reaction Mechanisms and Energy Applications,” Electrochem. Energy Rev., vol. 7, no. 1, p. 17, Dec. 2024, doi: 10.1007/s41918-024-00215-y.